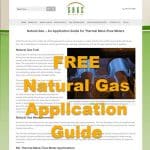
Natural gas measurement is where Sage thermal mass flow meters excel. There are various applications where the natural gas flow rate is needed, particularly in industrial plants. Below are some of the applications thermal mass flow meters are used to measure natural gas flow.
Natural Gas Measurement
Consumption
In today’s world, we are all becoming more aware of energy consumption and investigating methods for improving efficiency. The first step to improving efficiency is establishing a baseline by determining the natural gas usage, and thermal flow meters are ideal for this application.
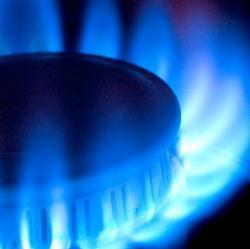
Efficiency
Combustion sources may have different efficiencies. By measuring the natural gas flow rate, the user can determine which operation is more efficient. A Sage thermal mass flow meter is the perfect solution for measuring natural gas flow rates to individual combustion sources. Read Four Ways Thermal Mass Flow Meters Can Save Natural Gas.
Greenhouse Gas Emissions
EPA 40 CFR Part 98 requires that major emitters report greenhouse gas emissions from their combustion sources. While multiple methods are permitted, the simplest is to measure the total amount of natural gas consumed and use EPA formulas to convert gas consumption to the various greenhouse gases emitted.
Measurement and Monitoring
Today, energy utilization and improving efficiency are primary objectives for most industrial facilities. We explore the topic at length in a new Sage Metering white paper. Here I share critical areas where thermal flow meters help the natural gas measurement and monitoring in industrial processes.
Natural Gas Efficiency
Stationary fuel combustion units have different efficiencies, and when measuring the natural gas flow rate at a source, one can determine which operation is more efficient. A thermal mass flow meter effectively measures natural gas flow rates to various combustion sources.
Submetering
When a plant is interested in energy conservation, a common practice submetering. It becomes necessary to monitor the natural gas flow rate and consumption at individual zones. Submetering helps in cost allocation to the different operating areas. It also helps the facility’s energy manager identify high consumption areas and unusual consumption points to promote conservation.
Combustion Efficiency
One unique method to reduce energy utilization in an industrial environment is optimizing combustion units’ combustion control. The optimal air-to-fuel ratio can be achieved when monitoring the air and fuel rates to the burners. This significantly reduces natural gas (or propane) costs and improves process efficiency, product quality, and yields.
Building Management Systems
Thermal mass meters are often used in building management systems for climate control. Insertion style flow meters for larger natural gas lines and in-line thermal mass flow meters for smaller gas lines may monitor the combustion source’s inlet flow.
Natural Gas Flow from the Main into Facility
Monitoring the plant’s natural gas mass flow rate provides information about the factory’s fuel demand. The standard billing meter only reports consumption over a particular period (i.e., monthly). A thermal mass flow meter monitors the flow rate and utilization. It also provides real-time feedback on operating conditions, peak demand, inefficiencies, and lost energy.
Sage Natural Gas Meter
Compared to other flow measurement technologies, the Sage Thermal Flow Meter obtains mass flow measurement without the need for temperature and pressure correction. The Sage meters provide excellent rangeability, outstanding low flow sensitivity, and no pressure loss. Also, the insertion probe is easy to install directly into the pipe. Other flowmeter types may require increased installation costs to reduce the pipe size when retrofitting existing equipment.
When working in a hazardous area, note that the equipment must have appropriate agency approvals.