Many different gases are used in steel production, including natural gas, oxygen, argon, and nitrogen. A central facilities department may want to submeter the gases to charge the various operations or conserve gas consumption throughout the mill. Whatever the reason, thermal mass flow meters are suitable in any of these applications. In many applications, a minimum amount of gas flow is required for the process, and lower gas usage can affect the product. In these cases, a flow meter can measure the gas flows, which will ensure that the optimum amount of gas is utilized.
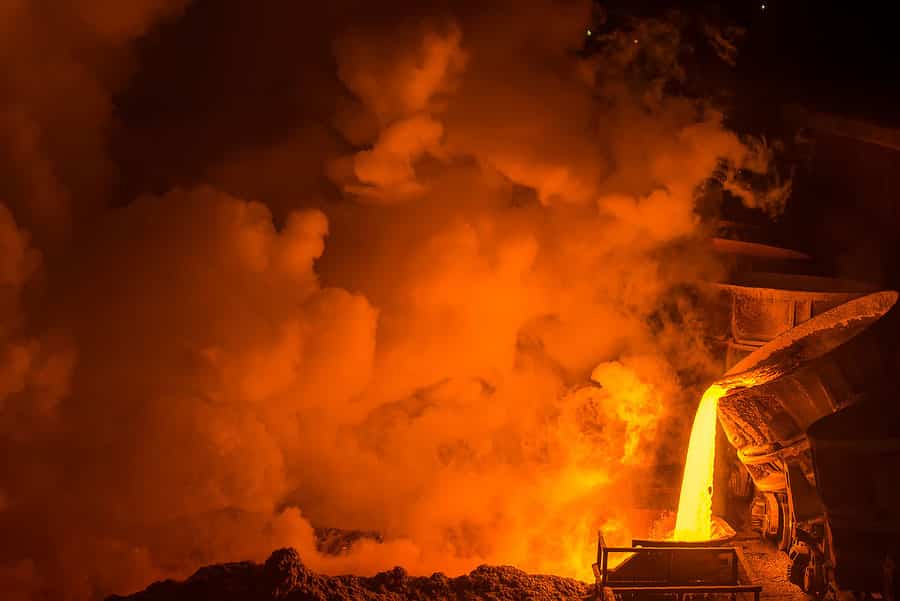
Basic Oxygen Furnace
The basic oxygen furnace (BOF) takes the basic pig iron from the blast furnace, mixes it with scrap, and then adds oxygen to reduce the carbon content. The reaction of oxygen and carbon releases heat and waste gases (carbon monoxide (CO) and carbon dioxide (CO2)) from the BOF. The CO-rich gas can be a fuel source for a waste heat boiler or combusted and flared. The steel from the BOF can then be further refined. Argon may be used for gas shrouding of the tuyeres, and argon and nitrogen can be used for bottom stirring to increase mixing. Some steels have specifications on acceptable nitrogen levels, thus requiring the use of argon in these instances.
Electric Arc Furnace
Electric arc furnaces (EAF) are in mini-mills. Here, scrap metal is loaded into the furnace. Electrical power applied to the electrodes creates heat and starts the melting process. In addition to the electrical energy, chemical energy is also provided by injecting oxygen into the molten steel. Here, the oxygen reacts with various metals in an exothermic reaction to produce additional heat and create metal oxides. The metal oxides end up in the slag. Oxygen lancing into the molten steel also produces heat and reduces the carbon content when the oxygen reacts with carbon to produce CO. After the correct composition is obtained, the molten steel is transferred to a ladle where it goes to the continuous caster or for further refining for high-quality steel.
Ladle Preheat
Ladles move molten steel between steps in the steel-making process. The ladles are preheated above the melting point of steel using combustion from natural gas to avoid solidifying the molten steel. As with any combustion operation, efficiency can be improved by controlling the air-to-fuel ratio.
Argon-Oxygen Decarburization (AOD)
The steel used for stainless steel or other high-grade alloy requires further reduction of the oxygen content. This process is completed in argon-oxygen decarburization (AOD) vessel. Additional oxygen, mixed with argon, is injected into the AOD through a lance and the tuyere in the side of the vessel. The presence of argon mixed with oxygen enhances the reaction of carbon with oxygen, thus promotes carbon removal.
Bottom Stirring
Bottom stirring is accomplished by injecting an inert gas into the lower part of a vessel containing molten steel. This process increases the heat transfer in the melt resulting in energy savings. Also, the increased interaction between slag and melt increases the liquid metal yield. Argon is used for those steels which specify a maximum nitrogen content.
Tundish
A tundish is a refractory-lined vessel that sits on top of a continuous caster and regulates the flow of molten steel to the caster. A ladle is used to pour molten steel into the tundish. Depending on the type of steel being made, argon may provide an inert environment around the connections to the continuous caster. For some grades of steel, argon may also be injected through diffusers in the tundish bottom. In both instances, a flow meter will ensure the proper amount of argon is used.
Tundish Preheat
Heat is lost when using the tundish. Thus, it is necessary to replace the tundish periodically with a new heated unit. The cooler tundish is taken to the tundish preheater, where a combustion system using natural gas heats the tundish.
Annealing
Some grades of steel are annealed to reduce internal stress and increase its workability. The steel is heated and then slowly cooled under controlled conditions. For gas annealing, the steel is covered and maintained under a nitrogen atmosphere to prevent oxidation. A nitrogen/hydrogen blend will decrease annealing time as hydrogen has a high heat capacity. For some grades of steel, annealing occurs with 100% hydrogen.
Furnaces
In addition to the electric arc furnaces (EAF) or basic oxygen furnace (BOF), there are multiple furnaces in a steel mill used for various operations. These may include process heaters, reheat furnaces, annealing furnaces, and tempering. These heating devices are usually fired using natural gas. There are many reasons why the measurement of the natural gas flow rates to these combustion sources is desirable, including efficiency determination and energy reduction programs.
Ingot Casting Line
High-grade quality steel is subject to oxidation when exposed to air. The ingots may be cast in an inert gas environment to avoid oxidation. Argon is preferred over nitrogen since nitrogen levels must be minimized in some quality steel.
Flare
The waste gases from the coke oven, blast furnace, and converters (EAF, BOF, and AOD) are frequently used as fuel gas. The gas from the coke oven typically consists of hydrogen (50 to 60%), methane (15 to 30%), and a small percentage (10 to 20%) of carbon monoxide, carbon dioxide, and nitrogen. The gas from the blast furnace and converters is carbon monoxide rich. These gases can be burned in an engine to produce supplemental power for the steel mill. In other cases, the gases might be flared. The EPA requirement for greenhouse gas emission reporting from a flare in a steel mill is the same as petroleum refineries which often include thermal mass flow meters measuring the gas flow to the flare.
If you would like more information on thermal mass flow meters, read What is a Thermal Mass Flow Meter?