Optimize Air to Fuel Ratio for Process Efficiency
One of the most important ways to reduce energy consumption in a manufacturing environment is to optimize the combustion control on industrial boilers, steam generators, and process heaters. One can achieve optimal air to fuel ratios by monitoring burners’ air and fuel rates. This practice significantly reduces natural gas (or propane) energy costs and improves process efficiency, product quality, and yields.
Environmental Regulation and ISO 50001
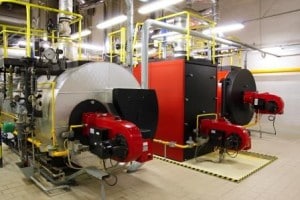
When tuning burners to reduce excess fuel usage, emissions are reduced, and energy is saved. As part of an overall strategy to mitigate plant-wide emissions, many local and state-wide jurisdictions have environmental regulations that require flow meters on all medium and large-size heating units. In addition, the newly promulgated ISO 50001 standards define the best practice for energy management, and fuel line monitoring will play a significant role. Typical applications for fuel line flow monitoring are in many industries, including textile, glass manufacturing, automotive, aluminum & steel, food & beverage, pulp & paper, power, chemical, and refining.
Thermal Flow Meters
Thermal mass flow meters are ideal instruments for this application. The Sage Prime provides both easy-to-install insertion thermal mass flow meters and in-line thermal flow meters, with built-in flow conditioners that monitor the burner’s air and fuel flow rates. These direct mass flow meters do not require separate temperature or pressure transmitters, have no moving parts, are highly accurate and repeatable, and have negligible pressure drop. The Sage Thermal Mass Meters have extraordinary rangeability of at least 100 to 1 and fast response. In addition to the 4 – 20 mA control output of flow rate, the meters also provide pulsed outputs of consumption, in conjunction with fully Modbus compliant RS485 RTU communications. The meters also feature bright graphical displays of flow rate, a non-resettable totalizer (often a requirement for environmental reporting), a temperature reading, plus continuous diagnostics. For difficult-to-reach burner lines or locations with extreme radiant heat, Sage offers a remote-style flow meter with up to 1000 feet of lead-length compensated cable. All electronics and power are at the transmitter – thus, the probe or flow body has a terminal junction box.