Here is a comprehensive review of the fundamentals of thermal mass flow measurement by a leading high-performance mass flow meter manufacturer, explaining why pressure and temperature correction are unnecessary when measuring with thermal mass flow meters (among many other things).
Thermal Mass Flow Measurement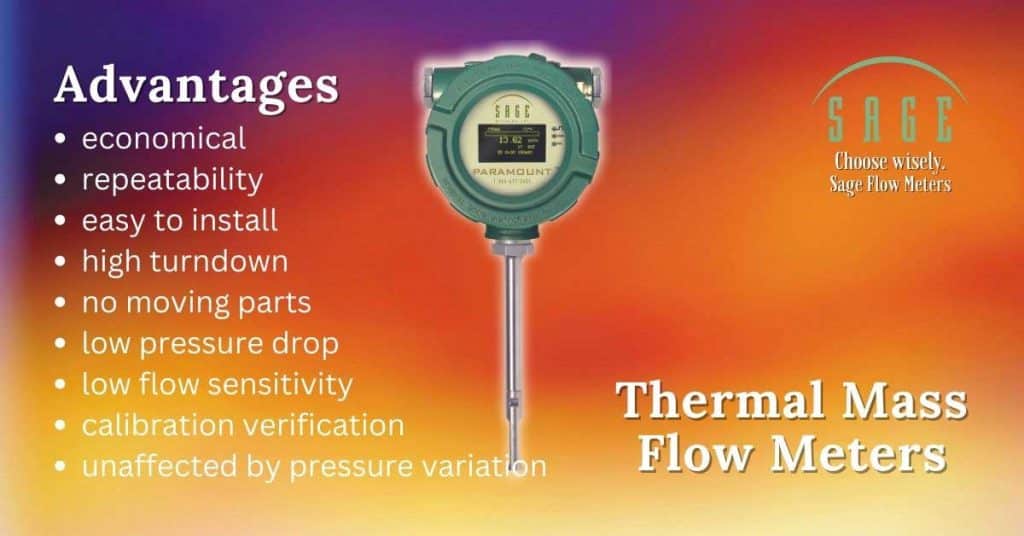
Thermal Mass Flow Measurement
As the manufacturer of Sage Metering thermal mass flow meters, we are often asked the following:
-
- Why do I need to measure mass flow?
- What is the difference between actual cubic feet per minute (ACFM) and standard cubic feet per minute (SCFM)?
- What is the theory of thermal mass flow quantification?
- Why are pressure and temperature corrections not required when using a thermal mass meter?
- What are the typical applications for using a thermal mass flow meter?
We take on these questions and more in our white paper. Download the PDF of the original white paper.
Actual Flow versus Standard Flow
Gas is compressible – this is one of the reasons the accurate measurement of gas flow rates is difficult. As the temperature increases, the gas molecules move further apart. Conversely, as the pressure rises, the gas molecules move closer together. Most gas flow meters (differential pressure, turbine, positive displacement, vortex shedding) measure the gas flow at the actual operating conditions where the measurement is made. This flow rate is frequently called ACFM (Actual Cubic Feet per Minute). However, what is more important is the flow rate adjusted or corrected for a particular pressure and temperature. This flow rate is frequently referred to as STP (Standard Pressure and Temperature) and is often measured in units of SCFM (Standard Cubic Feet per Minute).
Most gas flow meters require pressure and temperature correction to convert the flow rate from actual operating (ACFM) to standard (SCFM) conditions. Thus to get the mass flow rate of gas in standard conditions, measurement of the actual flow rate at operating conditions, the operating pressure, and the operating temperature are required.
Thermal Flow Measurement
A thermal mass flow meter is a precision instrument that measures gas mass flow. It represents an entirely different method for measuring flow rate. These meters measure the heat transfer as the gas flows past a heated surface. The gas molecules create heat transfer; the greater the number of gas molecules in contact with the heated surface, the greater the heat transfer. Thus, this flow measurement method depends only on the number of gas molecules and is independent of the gas pressure and temperature.
Figure 1 is an illustration of the sensor used by Sage Metering.
The Sage meter consists of two high-precision platinum sensors protected in a stainless steel covering. The temperature sensor is the reference and also measures the gas temperature. The flow sensor is heated to maintain a slight temperature difference (overheat) above the temperature sensor. As gas flows past the heated flow sensor, heat transfer occurs. The instrument measures the amount of power required to recover the desired overheat, which is proportional to the mass flow rate. The amount of energy in the form of heat to the sensor is very low, permitting using this technology in natural gas, hydrogen, or other flammable gases.
Thermal Mass Flow Meters
Thermal mass flow measurement is an inferred flow measurement. These meters measure heat transfer and then relate the heat transfer to the mass flow rate from the NIST traceable calibration. While calibrating the flow meter, a known amount of gas is run past the sensor, and the signal is measured. This is performed multiple times over the operating range of the instrument. A curve showing signal vs. flow rate is created for each meter. Figure 2 illustrates a typical curve.
Benefits of Thermal Mass Flow Meter
Thermal Mass Flow Measurement provides the benefits of:
-
- Mass flow measurement without the need for pressure and temperature correction
- Excellent sensitivity even at low flow rates
- High turndown capabilities
- Easy installation
- No moving parts ensure high reliability
7 Common Applications
Thermal mass flow meters are used in a broad range of applications. Here are seven common examples of using thermal flow meters:
#1. Natural Gas to Combustion Sources
Combustion sources such as boilers and furnaces have different efficiency. The user can determine the more efficient operation by measuring the natural gas flow rate to a combustion source. The thermal mass flow meter is ideal for measuring natural gas flow rates to individual combustion sources.
#2. Natural Gas Submetering
In facilities with different cost centers, submetering natural gas is frequently performed for cost allocations. When the cost of utilities is allocated to the various departments, there is an increased incentive to improve efficiency and reduce natural gas usage.
#3. Compressed Air
Industrial air compressors use more electricity than most other industrial equipment and account for as much as a third of the energy consumption in a plant. A thermal mass flow meter helps determine the optimal number of compressor units needed. Additionally, air leaks waste up to 30% of the industrial compressor’s output. Thermal mass flow meters help define the extent of leakage in a system and quantify the lost energy. For more information, read “ISO 50001 Energy Management: The Use of Thermal Mass Flow Meters in ISO 50001 Energy Management Systems.”
#4. Biogas Production
Biogas is produced in landfills as landfill gas and in anaerobic digesters as digester gas, among other places. It is high in methane and is often the focus of biogas-to-energy projects. An accurate gas flow measurement, whether monitoring, biogas destruction, or cogeneration, is needed throughout the production. Specific gas flow is also necessary for GHG emissions reporting to environmental agencies and carbon credit programs. Read “Digester Gas Flow at Wastewater Treatment Plants” or “Landfill Gas Monitoring, Recovery, and Flaring.”
#5. Flare Gas
Flare gas measurement and monitoring are necessary to ensure the system operates correctly. This application is complicated by varying gas compositions. To learn more, read “Flare Gas Measurement Using Thermal Mass Flow Meters.”
#6. Aeration Air
The activated sludge process is used at wastewater treatment plants to treat sewage and industrial wastewater. Microorganisms require Air flow to break down organic waste in this process. An optimum air flow throughout the system, sufficient to encourage waste consumption by the microorganisms (yet not excessive), is continuously sought.
#7. Combustion Air
Optimizing air-to-fuel ratios through accurate and repeatable gas flow measurement achieves combustion efficiency and energy management. Direct measurement of combustion air flow and fuel flow provides the criteria for peak efficiency. For more information, read “Combustion Efficiency and Thermal Mass Flow Meters.”
Conclusion
Since gas is compressible, its volume changes under pressure or when heated (or cooled). Thermal mass flow measurement is based on heat transfer and measures mass flow, not volumetric flow, and thus does not require temperature or pressure correction.
If you want more information on the benefits of thermal mass flow meters, these Sage in the Flow blogs may be of interest: