Recently, Flow Control published a Q&A regarding thermal mass flow measurement after corresponding with Wayne Shannon, Sage Metering Product Marketing Manager. In this Q&A, various topics were tackled, including the technology’s pros and cons, end-user challenges, application acceptability, and installation best practices.
To summarize, here is a reader’s digest version of the Q&A conversation:
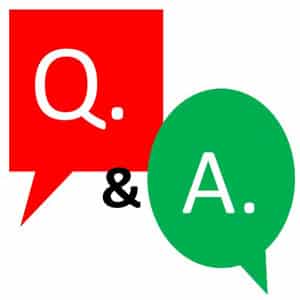
What are the limitations of this flow measurement?
-
- Can only measure the gas the manufacturer calibrated the meter
- Not accurate when measuring wet gas
- Variability during periods of rapid temperature changes
Which applications are most suitable for thermal flow meters?
-
- Measuring natural gas flow to combustion sources for energy management and environmental reporting
- Submetering natural gas for cost accounting, process efficiency, as well as tenant billing
- Air flow measurement for combustion air or compressed air
Common pitfalls encountered when using thermal flowmeters?
-
- End-user overlooks the length of the straight run, which impacts the flow profile
- The flow profile in the installation must be the same as the calibration flow profile
Critical challenges for using thermal flow meters in flare gas measurement?
-
- Rapid changes in flow rates and carry over material
- Change in gas composition at refineries and petrochemical plants
How can an end-user ensure the meter best matches the needs of the application?
-
- Provide the flow meter manufacturer the ranges of flow rate and temperatures, pressure, gas composition, and piping system description, including pipe’s straight run and disturbances.
For a further explanation on any of these questions, as well as a glimpse of what the future technology holds, read “All You Ever Wanted to Know about Thermal Flow Meters.” Additionally, our article, “How to Overcome Thermal Flow Meter Limitations,” tackles nine thermal flow meters’ limitations and how to address them.
Image by Peggy und Marco Lachmann-Anke from Pixabay