We conclude this combustion efficiency series by explaining that thermal mass flow meters are ideally suited as a natural gas flow meter and as a combustion air flow meter for industrial heat sources, such as industrial boilers, steam generators, furnaces, ovens, smelters, and process heaters.
Air Flow Meter
Thermal mass flow meters are ideal for measuring natural gas flow and combustion air flow in combustion processes.
Questions? Let us know how we can help.
Principals of Thermal Mass Flow Meter Operation
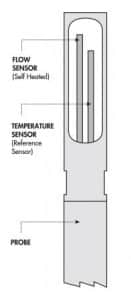
Thermal mass flow meters measure gas flow based on the principle of convective heat transfer. Either insertion-style probes or in-line flow bodies support two sensors that are in contact with the gas. The sensors are resistance temperature detectors (RTDs), and the Sage Metering sensors consist of highly stable reference-grade precision-matched platinum windings that are clad in a protective 316 SS sheath for industrial environments.
One of the sensors is heated by the circuitry and serves as the flow sensor, while a second RTD acts as a reference sensor and measures the gas temperature. The SAGE proprietary sensor drive circuitry maintains a constant overheat between the flow sensor and the reference sensor. As gas flows by the heated sensor (flow sensor), molecules of the flowing gas transport heat away from this sensor, the sensor cools, and energy is lost. The circuit equilibrium is disturbed, and the temperature difference (ΔT) between the heated sensor and the reference sensor has changed. Within one second, the circuit will restore the lost energy by heating the flow sensor, so the temperature is restored.
The electrical power required to maintain this overheat represents the mass flow signal. There is no need for external temperature or pressure devices.
An advantage of thermal flow meters is that they have no moving parts, which reduces maintenance. It also permits their use in trying application areas, including wet (saturated) gas. They also do not require temperature or pressure corrections and provide excellent overall accuracy and repeatability over a wide range of flow rates. This meter style measures mass flow rather than volume and is one of the few categories of meters that can measure flow in large pipes and ducts.
Sage provides thermal mass meters that are factory calibrated and configured for easy installation. They can be installed directly into the pipe or duct without needing field setup and calibration. Sage offers insertion and in-line thermal mass flow meters with intrinsic flow conditioners that monitor the air and fuel flow rates to the burner. These direct mass flow meters are highly accurate and repeatable and have negligible pressure drop.
The Sage meter has an outstanding rangeability of at least 100 to 1 and has the rapid response needed for complete combustion control. Because of its low-end sensitivity, the Sage thermal mass flow meter can accurately measure extremely low velocity, down to 5 SFPM, making it highly effective for measuring the low flow rates of air and natural gas, which can occur at low boiler operating loads. In addition to the 4 – 20 mA control output of flow rate, the meters also provide pulsed consumption outputs and Modbus-compliant RS485 RTU communications. The meters feature bright graphical displays of flow rate, totalized flow, gas temperature, and continuous diagnostics. For hard-to-reach burner lines or locations with extreme radiant heat, SAGE also offers a remote-type flow meter with up to 1000 feet of lead-length compensated cable. In the remote meter, all electronics and power are at the transmitter – thus, the probe or flow body simply has a terminal junction box.
Thermal mass flow meters provide a reliable solution to measure gas mass flow for different environmental applications. As previously stated, the EPA requires reporting greenhouse gas emissions from various stationary combustion sources. When burning natural gas, biogas, or other gaseous fuels, the simplest method of determining greenhouse gas emissions is to measure the amount of fuel consumed and then use EPA formulas to convert the fuel consumption to emissions of the various greenhouse gases. The SAGE meter fully complies with EPA reporting requirements using the built-in totalizer and meets EPA calibration requirements.
Calibration Verification
The SAGE TMFM comes from the factory fully calibrated and can easily verify that it maintains its original factory calibration through an in-situ calibration verification.
The Sage Prime and Paramount meters can perform the in-situ calibration check if a “no-flow” (0 SCFM) condition is created. “No flow” is easily created using an isolation valve assembly with the insertion meter type. Unlike other TMFMs, the SAGE In-Situ Calibration not only verifies that the unit is accurate; it also indicates that the sensor is clean. If the meter does not pass the calibration test the first time, in most cases, simply cleaning the sensor and re-testing will confirm that the meter is accurate and hasn’t drifted or shifted.
Conclusion
By assessing stoichiometric combustion, we know the parameters needed to achieve optimum combustion to save energy, increase efficiency, and reduce pollutants. We achieve combustion efficiency and energy management by optimizing air-to-fuel ratios attained through accurate and repeatable gas flow measurement. Direct measurement of combustion air flow and fuel flow provides the criteria for maximum efficiency. Thermal mass flow meters are ideal for measuring the mass flow of combustion air and fuel gas, outperforming traditional flow meters in these applications.
If you want to read this report in full, follow the Sage Metering white paper Combustion Efficiency and Thermal Mass Flow Meters.
Air Fuel Ratio Effect Combustion Efficiency and Air Fuel Ratio