In part three of this series on combustion control, we consider flue gas oxygen and combustibles and varying air and fuel pre-combustion flows to improve industrial boilers’ combustion efficiency, steam generators, furnaces, ovens, smelters, and process heaters. We also show that mass flow measurement of natural gas and combustion air flow provides essential information for a facility to operate at maximum efficiency and minimal emissions.
Flue Gas
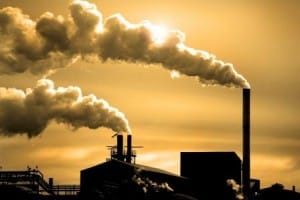
By understanding the delicate balance of excess air-and-fuel usage, we can measure both the concentrations of oxygen and combustibles in exhaust gas to generate an air-to-fuel control strategy. The measurement of both O2 and CO is critical measurements here. Measurements of both flue gas oxygen and combustibles are required to maintain combustion efficiency continuously.
When determining the carbon monoxide content from the flue gas, we can adjust the operation because the CO content represents the unburnt fuel, which is wasted because of insufficient air. Alternatively, by measuring the O2 in the stack gas, we can monitor energy loss from too much excess air.
Oxygen and combustible analyzers can provide continuous sampling and analysis of flue gases, making analyzing oxygen and combustibles in the stack gases a way to maximize combustion efficiency. Optimum combustion can be achieved at various air-to-fuel ratios to correspond with different operating loads. This makes it challenging to use oxygen analyzers alone to control excess air. Additionally, an uneven oxygen supply in the flue gas could result in variations in oxygen levels.
Measuring Air and Fuel Flow
In the previous section, we explored using flue gas measurements to control the air-to-fuel ratio; here, we examine varying air and fuel pre-combustion flow to improve efficiency. Burner management systems optimize the air-to-fuel rate for maximum efficiency and minimal unburnt combustibles. A ratio flow strategy is crucial in the safe and cost-effective operation of fired heaters, furnaces, boilers, and similar combustion processes. The first requirement is to determine process variable signals by measuring the mass flow of the gas and combustion air flow rate. Since mass dictates combustion, measuring mass flow rather than volumetric flow is optimal.
Mass flow measurement of natural gas and combustion air flow provides essential information for a facility to operate at maximum efficiency and with minimal emissions.
Air Flow Monitoring
Measuring combustion air flow can be difficult because it is customary to have high flow rates at low pressures through irregular and large ducts. Swirls and turbulence, combined with insufficient straight runs, make it challenging to achieve the desired flow profiles, which can vary with different operating loads.
The meter must be in calibration and have good repeatability. Tuning the boiler optimizes combustion efficiency. During combustion tuning, the air-to-gas fuel rates are optimized at different boiler loads. Tuning includes measuring air and gas mass flow rates along with O2 and CO concentration, NOX concentration (if appropriate), outlet temperature, and flue-gas recirculation flow settings (if applicable). In air flow monitoring, the combustion air flow is tuned to match the gas flow to achieve the desired air-to-gas ratio when setting the fuel flow. The meter must provide repeatable flow measurements when operating at the same parameters on a different day.
Natural Gas Measurement
Measuring natural gas flow to the combustion source can be used to improve overall combustion efficiency.
There is also a need to measure greenhouse gas emissions to comply with EPA requirements. Facilities emitting 25,000 metric tons of CO2e annually are required by the EPA to report annual emissions per EPA mandate 40 CFR Part 98. Additionally, local environmental authorities often require reporting natural gas consumption to determine emissions.
In part four of this combustion control series, we evaluate various flow technologies used in measuring gas flow, noting that few excel in combustion air flow measurement. If you are interested in reading more on this subject, you may be interested in the Sage Metering white paper Combustion Efficiency and Thermal Mass Flow Meters.