In part two of this series on combustion control of industrial heat sources, we consider the air-fuel ratio and the balance of using excess air to consume combustibles while minimizing energy from going up the stack in industrial heating sources. In Part I, Stoichiometric Combustion and its Impact on Boiler Efficiency, we discussed stoichiometric combustion, the theoretical position of the optimal amount of oxygen and fuel mixture to produce the most heat possible while achieving maximum combustion efficiency.
Ask how our flow meter can improve your energy management.
Air Fuel Ratio and Excess Air
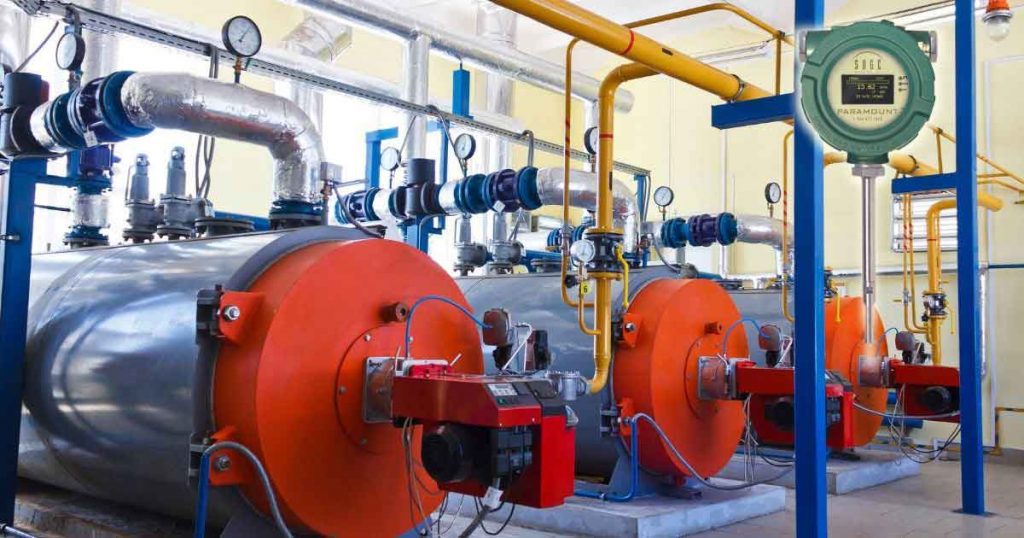
In fuel-fired process heating, the largest energy loss source is the exhaust stack, so managing airflow is essential to combustion efficiency. When fuel burns in the presence of oxygen, it converts to carbon dioxide, water, and heat. Consider the combustion of methane (CH4).
CH4 + 2O2 → CO2 + 2H2O + Heat (1,013 Btu/ft.3)
Air contains approximately 21% oxygen and 79% nitrogen. In this case, the reaction for complete combustion becomes:
CH4 + 2O2 + 7.53N2→ CO2 + 2H2O + 7.53 N2 + Heat (1,013 Btu/ft.3)
The amount of air required will vary depending on the type of fuel. Ideally, you would like to add enough oxygen to consume all the fuel so that little or no combustibles are exhausted while minimizing the excess air to prevent energy loss out of the stack.
The air-to-fuel ratio defines the amount of air needed to burn a specific fuel. The conventional fuels used in the combustion process are oil (#2, 4, and 6), diesel oil, gasoline, natural gas, propane, and wood—ratios for common gases, liquid, and solid fuels noted in Tables 1.1 and 1.2.
Optimizing Air-to-Fuel Ratio
There is a balance between losing energy from using too much air and wasting energy from running too richly in any combustion process. The best combustion efficiency occurs at the optimum air-to-fuel ratio, and controlling this provides the highest efficiency. A liquid and gas fuel burner achieve this desired balance in most scenarios by operating at 105% to 120% of the optimal theoretical air. For natural gas-fired burners, the stoichiometric air required is 9.4-11 ft.3 / 1.0 ft.3 of natural gas or approximately an air-to-gas ratio of approximately 10:1. In this case, there is an excess oxygen level of 2%.
In the combustion zone, it is challenging to measure excess air. However, in the stack, it can be easily measured using Oxygen analyzers. Operating with 5%-20% excess air would correspond to a 1% to 3% oxygen measurement in the stack.
The ideal air-to-fuel relationship will vary at different operating loads. Tuning is the act of establishing the desired air-to-fuel relationship under various operating conditions. It can be accomplished when evaluating specifics in the stack: temperature, oxygen concentration, carbon monoxide, and NOx emissions.
In part three of this five-part series, we consider analyzing flue gas oxygen and combustibles, along with varying air and fuel pre-combustion flows, to improve the combustion efficiency of industrial boilers, steam generators, furnaces, ovens, smelters, and process heaters.
If you are interested in reading the Sage Metering white paper on this topic, see Combustion Efficiency and Thermal Mass Flow Meters.
Boiler Combustion Efficiency Explained
Air Flow Meter for Combustion Efficiency | Industrial Boilers