In part one of this five-part series, we discuss stoichiometric combustion, the theoretical position in which the optimal amount of oxygen and fuel mix produces the most heat possible while achieving maximum combustion efficiency for industrial boilers.
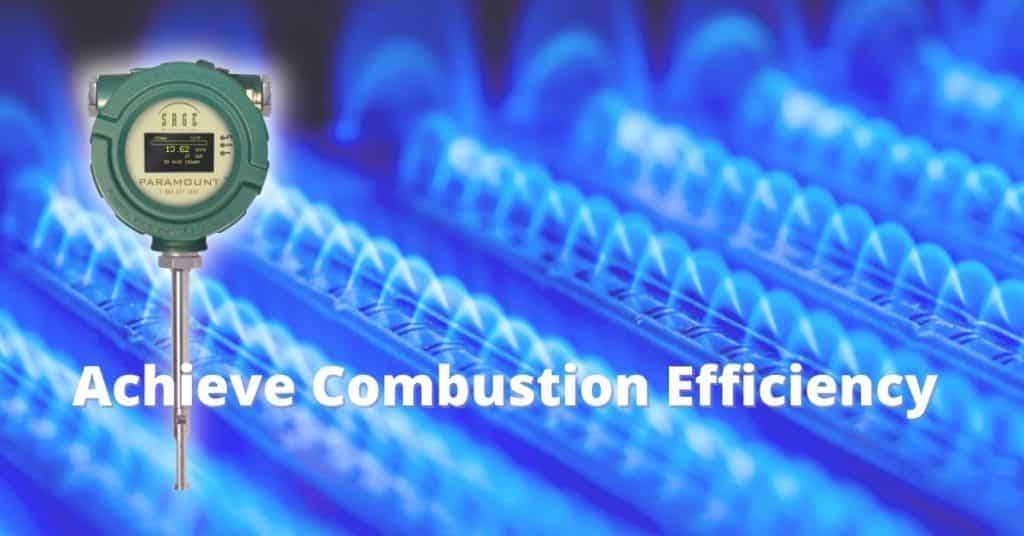
Combustion Efficiency
A significant way to reduce energy consumption in a manufacturing environment is to optimize the combustion control on industrial boilers, steam generators, furnaces, ovens, smelters, and process heaters. We achieve combustion efficiency and energy management through accurate and repeatable measurements of gases.
Combustion Control
By monitoring the air and fuel rates to burners, optimal ratios are achieved, resulting in significant reductions in fuel gas cost, improved process efficiency, enhanced product quality, and better yields while simultaneously lowering combustibles. Many local and state-wide jurisdictions have environmental regulations requiring flow meters on medium and large heating units to measure plant-wide emissions. Typical applications for combustion control monitoring are found in various industries, including textile, glass manufacturing, automotive, aluminum & steel, food & beverage, pulp & paper, power, chemical, and refining.
Stoichiometric Combustion
The purpose of combustion is to consume fuel efficiently to produce heat. There are three components of combustion: fuel, oxygen, and heat. The most common fuel sources in the combustion process are fossil fuels, natural gas, oil, and coal. Fossil fuels are hydrocarbons, organic compounds containing carbon and hydrogen. To maximize combustion efficiency, it is vital to consume (or burn) all the fuel, which is known as complete combustion.
It is essential to introduce air into the combustion chamber to achieve complete combustion. Without it, the fuel will have limited or incomplete combustion, and the exhaust gases will include some unburnt and partially burnt fuel. Assuming we are evaluating a natural gas-fed combustion process, the unburnt fuel components will be carbon monoxide (CO), hydrogen (H2) as well as methane (CH4).
Combustion efficiency depends on using the right amount of air to consume the fuel.
Fuel Consumption
The presence of uncombusted or partially burnt fuel indicates incomplete combustion, which significantly reduces efficiency. Therefore, burning the fuel in excess oxygen ensures that the fuel will achieve complete combustion.
Excess Oxygen
All excess air heats in the combustion chamber during the combustion process, and this energy is lost out of the exhaust. For this reason, the next governing factor of combustion control is to minimize the extra oxygen used to reduce the loss of energy from heat going up the stack.
Stoichiometric combustion is a theoretical position where the optimal amount of oxygen and fuel mix generates the most heat possible, achieving maximum combustion efficiency. There are no unburnt combustibles and no excess air. It is something to strive for, though, in reality, it does not exist. It is theoretical, and in an actual combustion process, the mixing between the air and fuel does not support the best conversion.
In part two of this series, we will explore the balance of using excess air to consume combustibles while reducing energy loss up the stack. If you are interested in reading the Sage Metering white paper on this topic, see Combustion Efficiency and Thermal Mass Flow Meters.
Perhaps this video may be of interest:
Air Fuel Ratio Effect Combustion Efficiency and Air Fuel Ratio
Air Flow Meter for Combustion Efficiency | Industrial Boilers